10 Simple Techniques For Mfgs
Wiki Article
Oem - The Facts
Table of ContentsAn Unbiased View of Additive ManufacturingManufacturing Fundamentals ExplainedThe Of Die CastingThe Facts About Oem RevealedUnknown Facts About Lean Production
Then, the mould closes as well as the process repeats. Pre-moulded or machined parts can be placed right into the tooth cavity while the mould is open, permitting the product infused in the following cycle to form as well as solidify around them. This procedure is called Insert moulding as well as enables solitary components to consist of several products.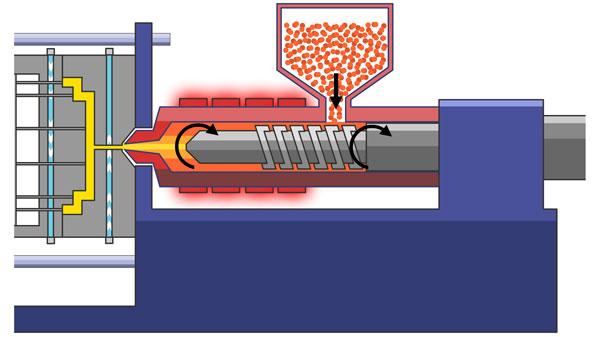
The plastic injection moulding industry has evolved for many years from creating combs and also buttons to producing a substantial range of items for lots of markets consisting of automotive, clinical, aerospace, customer products, playthings, plumbing, product packaging, and also construction.: 12 Examples of polymers ideal suited for the process [modify] A lot of polymers, occasionally referred to as materials, might be utilized, consisting of all thermoplastics, some thermosets, as well as some elastomers.
Available materials consist of alloys or blends of previously developed materials, so item designers can select the material with the most effective set of properties from a substantial choice. Major criteria for option of a material are the strength and also feature required for the final component, as well as the price, however also each material has various criteria for moulding that must be taken into account.: 6 Other considerations when choosing an injection moulding product include flexural modulus of flexibility, or the level to which a material can be bent without damages, as well as warm deflection as well as water absorption.
Getting The Lean Production To Work
Applications include buckles for securing and separating outdoor-equipment webbing. Tools [modify] Injection moulding makers contain a material hopper, a shot ram or screw-type bettor, as well as a heating unit.: 240 Additionally referred to as platens, they hold the moulds in which the components are formed. Presses are ranked by tonnage, which expresses the quantity of securing force that the equipment can apply.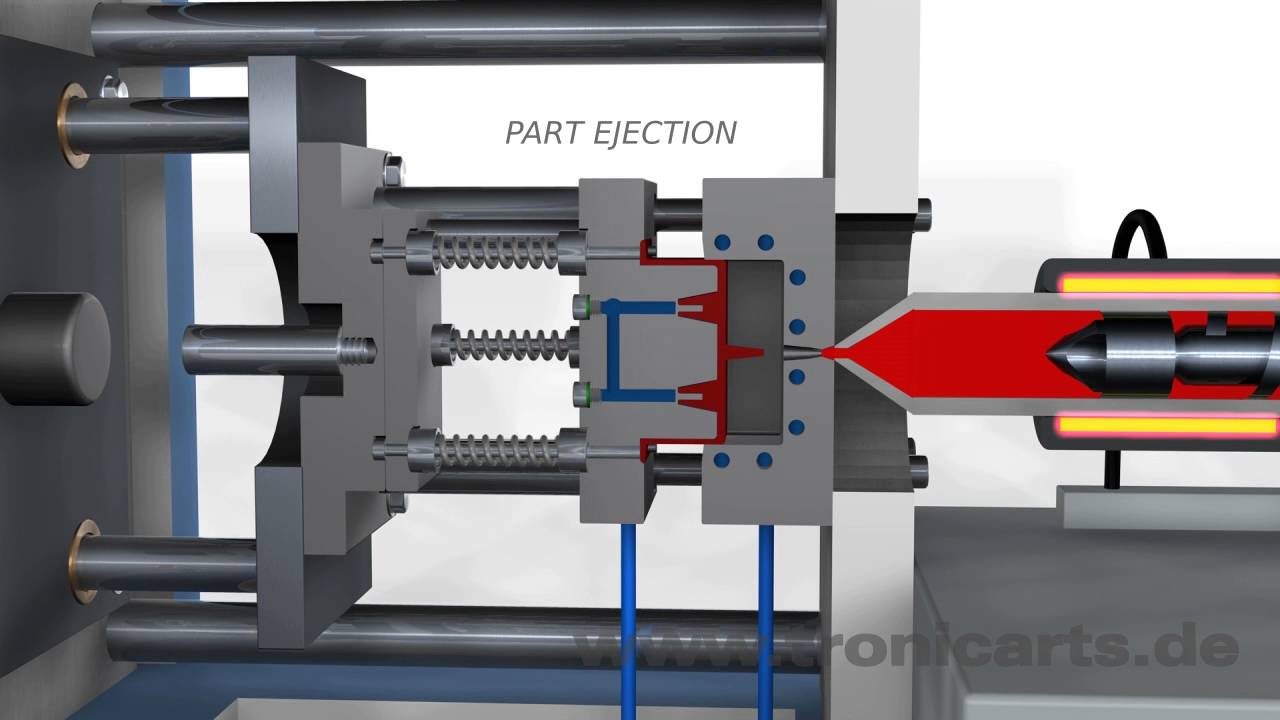

Mould or pass away are the typical terms used to describe the tool utilized to generate plastic components in moulding. Because moulds have actually been costly to produce, they were normally just utilized in automation where thousands of components were being created. Regular moulds are constructed from set steel, pre-hardened steel, aluminium, and/or beryllium-copper alloy.: 176 The selection of product to construct a mould from is primarily among economics; generally, steel moulds cost even more to construct, but their longer lifespan offsets the higher preliminary cost over a higher number of components made before wearing.
8 Simple Techniques For Plastic Manufacturing
Injection moulding die with side pulls "A" side of die for 25% glass-filled acetal with 2 side pulls. Close up of detachable insert in "A" side. "B" side of die with side pull actuators. Mould style [edit] Basic 2 plates tooling core as well as cavity are inserts in a mould base "household mould" of 5 different components The mould contains two primary elements, the injection mould (A plate) and the ejector mould (B plate).Plastic material gets in the mould through a or gateway in the injection mould; the sprue bushing is to secure firmly against the nozzle of the shot barrel of the moulding device and to enable molten plastic to stream from the barrel into the mould, likewise known as the cavity.: 141 The sprue bushing guides the molten plastic to the dental caries photos via networks that are machined into the faces of the An and B plates.
(A) Sprue, (B)&(C)runner and (D)gates in actual injection moulding item for toys The amount of resin required to fill up the sprue, jogger and also cavities look at here of a mould makes up a "shot". Trapped air in the mould can get away via air vents that are ground right into the parting line sites of the mould, or around ejector pins and also slides that are somewhat smaller than the openings preserving them.
The air can also come to be so compressed that it ignites as well as burns the bordering plastic material.: 147 To permit for removal of the moulded part from the mould, the mould attributes must not overhang each other in the instructions that the mould opens up, unless components of the mould are developed to move from in between such overhangs when the mould opens up using elements called Lifters.
Top Guidelines Of Plastic Manufacturing
The coolant takes in warmth from the mould (which has soaked up heat from the hot plastic) and maintains the mould at an appropriate temperature level to solidify the plastic at the most reliable rate.: 86 To alleviate upkeep and venting, cavities and cores are divided right into items, called inserts, as well as sub-assemblies, additionally called inserts, blocks, or chase blocks.Extra intricate parts are developed using extra complex moulds. These may have areas called slides, that relocation into a tooth cavity perpendicular to the draw direction, to create looming part features. When the mould is opened, the slides are retreated from the plastic part by using fixed "angle pins" on the stationary mould fifty percent. lean manufacturing.
The component is after that ejected and the mould shuts. The closing action of the mould causes the slides to relocate onward along the angle pins.: 268 A mould can generate a number of copies of the very same parts in a solitary "shot". The variety of "perceptions" in the mould of that part is typically incorrectly referred to as cavitation.
In many cases, several tooth cavity tooling moulds a series of different components in the very same tool. Some toolmakers call these moulds family members moulds, as all the components are relatede. g., plastic version kits.: 114 Some moulds enable previously molded components to be returned to enable find a new plastic layer to form around the first component.
See This Report on Additive Manufacturing
This system can permit production of one-piece tires and wheels. Two-shot or multi-shot moulds are designed to "overmould" within a solitary moulding cycle and also need to be processed on specialized shot moulding devices with 2 or more shot systems. This procedure is actually an injection moulding process carried out two times as well as for that reason has a much smaller sized margin of error.After that the 2nd material, a different colour, is injection-moulded into those areas. Pushbuttons as well as keys, for circumstances, made by this process have markings that can not wear off, and also remain understandable with heavy use.: 174 Mould storage space [edit] Makers most likely to great sizes to safeguard personalized moulds due to their high standard prices.
Report this wiki page